Condividiamo il bell’articolo realizzato da Industria Italiana Magazine sulle best practices dell’eccellenza industriale bresciana in termini di ricerca e innovazione. Le stesse presenti a Fabbrica del Futuro, il padiglione realizzato da Confindustria Brescia per uno sviluppo all’insegna della sostenibilità. Al suo interno l’intervista a Carlo Grazioli, che racconta la rivoluzione portata avanti da Gruppo Grazioli nel mondo della distribuzione industriale grazie a Stampa 3D e Additive Manufacturing.

Ricerca e innovazione alla Fabbrica del Futuro di Brescia.
Le best practice di Gruppo Grazioli, Feralpi, Beretta.
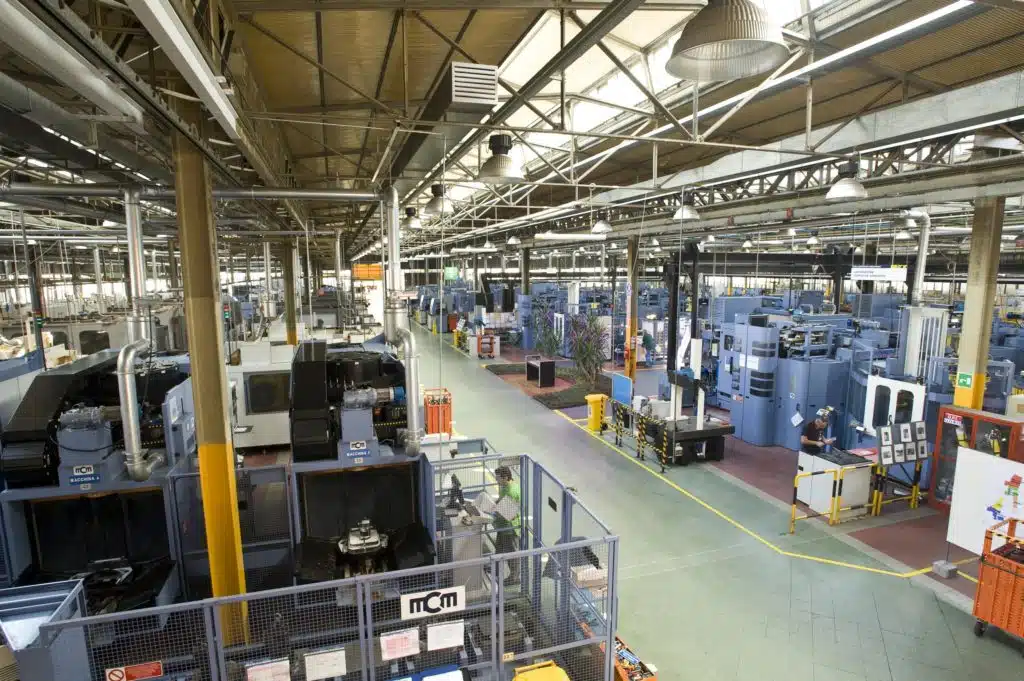
Con 10 miliardi di valore aggiunto e oltre 160mila occupati, Brescia è la capitale europea dell’industria. Il padiglione Parco dell’Acqua di Brescia della Fabbrica del Futuro è il centro delle iniziative della Confindustria locale. Trenta progetti divisi in sei temi: cultura d’impresa, ricerca e innovazione, sostenibilità, welfare, sinergia impresa-territorio. Andiamo alla scoperta dei tre progetti relativi a ricerca e innovazione. La Digital Factory Experience di Feralpi. I servizi di progettazione e stampa 3D di Feralpi. La Beretta Intelligent Factory, il progetto 4.0 di Beretta.
Dalle app per le visite virtuali negli stabilimenti di Feralpi Holding, una delle più grandi aziende europee di produzione di acciaio e prodotti derivati; alla Intelligent factory della fabbrica di armi Beretta che usa l’intelligenza artificiale per supportare i processi industriali a elevata complessità attraverso l’analisi dei dati, affiancando e valorizzando l’Intelligenza umana; fino al percorso di accompagnamento alla stampa 3d per l’industria realizzato dal Gruppo Grazioli, attivo nelle forniture industriali integrate e nato come metalmeccanica. Raccontiamo i tre progetti industriali della sezione ricerca e innovazione della “Fabbrica del Futuro”, padiglione inaugurato il 26 maggio nel Parco dell’Acqua di Brescia, pivot delle iniziative che Confindustria Brescia, guidata da Franco Gussalli Beretta (patron della già citata fabbrica d’armi), sta realizzando nell’ambito di Bergamo Brescia Capitale della Cultura 2023. Fabbrica del futuro diventerà il brand delle best practice dell’industria locale: e in effetti non potrebbe essere sorta in nessun altro luogo, perché Brescia, è la prima provincia industriale d’Europa sia per valore aggiunto (oltre 10 miliardi euro) sia per numero di occupati (oltre 160mila).
Fabbrica del Futuro: dov’è e di cosa si tratta.
Nel padiglione del Parco dell’Acqua la Fabbrica del Futuro è sintetizzata da 30 progetti, selezionati tra quelli presentati dalle oltre 1300 associate di Confindustria Brescia in un contest avviato lo scorso settembre. Più in dettaglio, i progetti sono raggruppati per temi (cultura d’impresa, ricerca e innovazione, sostenibilità, welfare, sinergia impresa-territorio).
Il padiglione – 195 mq di superficie, con uno spazio esterno di 68,25 mq è realizzato con portali di legno lamellare per la struttura portante, pannelli x-lam per solaio e travi portanti e policarbonato alveolare per il rivestimento, materiale sostenibile che verrà riciclato (tutte le specifiche tecniche sono disponibili nella scheda tecnica allegata al comunicato). L’installazione è realizzata dall’azienda bresciana Wood Beton, su progettazione dello studio Arw e con il contributo, per le tecnologie digitali, di innexHub. All’interno totem digitali che permettono ai visitatori di avere ogni spiegazione possibile sul progetto a cui sono interessati.
Feralpi: la fabbrica dell’acciaio diventa virtuale grazie alla realtà aumentata.
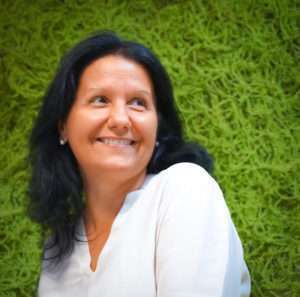
Feralpi è una siderurgia tra le più grandi di Europa, fondata nel 1968 a Lonato del Garda e specializzata nella produzione di acciai destinati sia all’edilizia sia ad applicazioni speciali, che trovano il loro impiego in particolare nell’automotive. Nel 2022 i ricavi sono ammontati a 2,39 miliardi (+24,4% anno su anno) e l’azienda progetta investimenti straordinari oltre i 500 milioni di euro nel piano industriale 2023-2027 per rafforzare l’impegno per un acciaio sempre più decarbonizzato con l’accelerazione della produzione di rinnovabili. Alla Fabbrica del futuro l’acciaieria partecipa con la Digital Factory Experience. «L’obiettivo del progetto è quello di offrire alla più ampia platea di stakeholder la possibilità di visitare virtualmente i plant produttivi del gruppo, con un approccio inclusivo e smart, bypassando le barriere fisiche e tecnologiche», spiega Isabella Manfredi, direttore comunicazione, relazioni esterne e sustainability manager Feralpi Group di Feralpi Group.
Il progetto nasce in epoca Covid 19 per limitare le visite in azienda e ridurre il rischio dei contagi. «L’accessibilità su device mobili “apre” le porte di Feralpi H24, 7/7.
Un’esperienza a 360° utilizzabile in ogni contesto: eventi, fiere, seminari, workshop, visite aziendali (tutorial pre-visita fisica nei reparti), attività di educational e engagement, supporto all’attività commerciale come preview del plant per i clienti – continua Manfredi – Il progetto è stato realizzato per i principali plant di Gruppo, ma estendibile potenzialmente ad ogni stabilimento. È in corso l’integrazione con la digital factory experience presso lo stabilimento tedesco di Feralpi Stahl. L’attività ha previsto: la mappatura delle aree, la definizione dei percorsi per i visitatori, la produzione di contenuti multimediali ad hoc in funzione degli obiettivi, la creazione di visite per singolo plant, una landing page dedicata e l’integrazione nel corporate website, estendibile ai siti delle singole società».
La realizzazione della piattaforma digitale ha facilitato la conoscenza del gruppo in occasione di grandi eventi nazionali e internazionali come touchpoint ed engagement per i visitatori (Made in Steel, Milano – Tube&Wire, Duesseldorf – Futura, Brescia) nonché per eventi interni di presentazione del Gruppo e conferenze stampa. Agganciato a google analytics e integrato nel corporate website ha accessi monitorabili per la definizione di KPI specifici. «In altre parole, lo strumento e i contenuti pubblicati favoriscono l’awareness di Feralpi Group indipendentemente dalla tipologia e dalla localizzazione dell’interlocutore, valorizzando l’impegno Esg del Gruppo (e rispettive perfomance) in linea con la corporate strategy di Feralpi».
Gruppo Grazioli, l’azienda che sta rivoluzionando il mondo della distribuzione industriale con la stampa 3D.
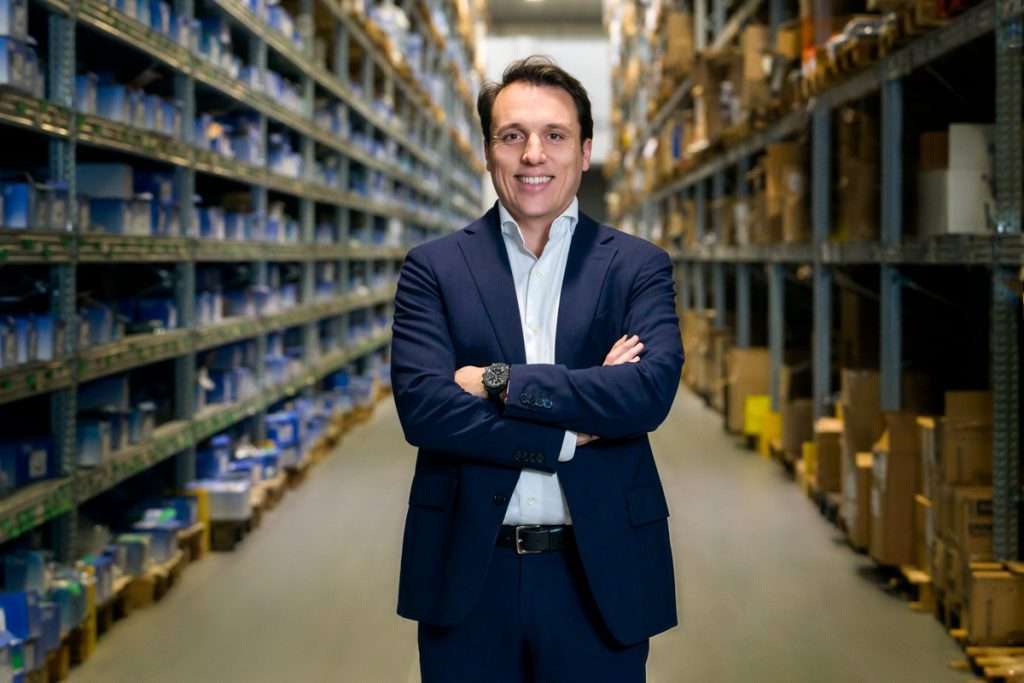
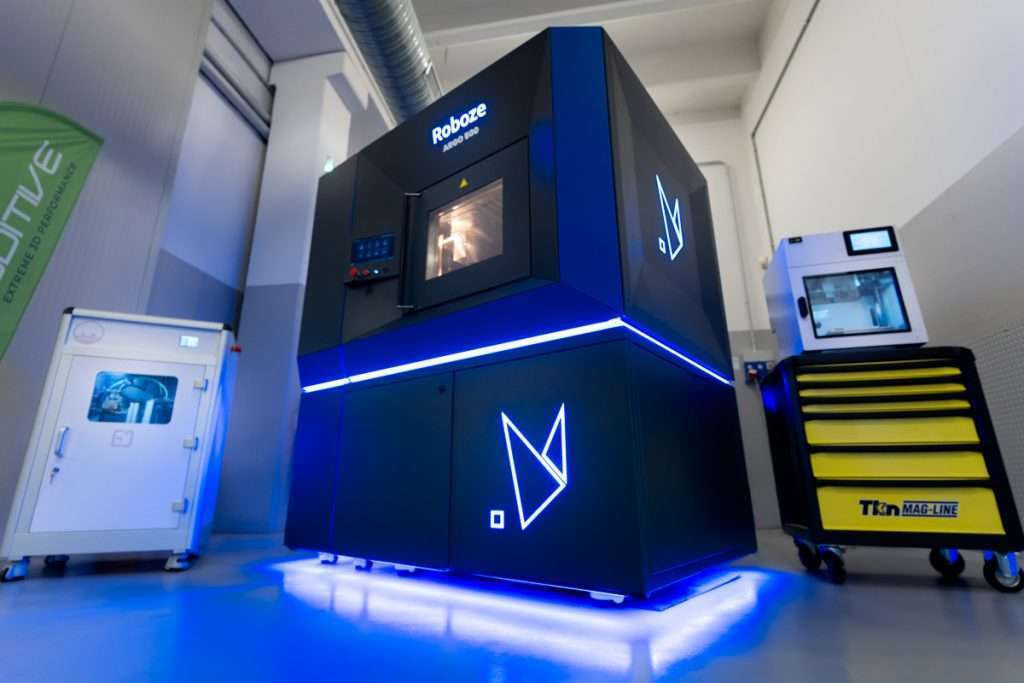
I collaboratori del gruppo sono circa 200 e il fatturato aggregato ha superato i 43 milioni di euro con un Ebitda di circa 2,8 milioni (dati 2021). Gruppo Grazioli, realtà nata nel 1875 come una ferramenta, nel corso degli ha cambiato pelle, concentrandosi sul settore industriale e ampliando l’offerta, con l’inserimento nuove piattaforme di prodotto: «Siamo cresciuti fino a diventare un gruppo di aziende di riferimento nella distribuzione industriale», dice Carlo Grazioli. Pur essendo cresciuta in termini dimensionali e di struttura organizzativa, la guida familiare di Gruppo Grazioli rimane un valore. «L’orientamento a lungo termine, la condivisione di cultura e valori, l’agilità decisionale sono fondamentali per il nostro successo. Questo ci ha permesso di rimanere agili e reattivi, adattarci rapidamente alle esigenze dei nostri clienti e anticipare alcune necessità di un mercato in continuo cambiamento. La missione del Gruppo Grazioli è quella di trasformare i processi tradizionali della distribuzione industriale. Forniamo i migliori prodotti disponibili sul mercato integrati a servizi personalizzati per generare efficienza, ridurre i costi e ottimizzare i tempi. Copriamo una vasta gamma di forniture industriali, dall’utensileria alle attrezzature meccaniche, dalla componentistica per impianti e manutenzioni ai dispositivi di protezione individuale. Il nostro approccio è orientato a studiare le esigenze specifiche di ogni azienda cliente e proporre le soluzioni migliori per ogni applicazione».
Parte integrante dell’offerta di Gruppo Grazioli sono dunque i servizi, che includono progettazione e stampa 3D. «Il nostro ufficio tecnico di progettazione ci consente di sviluppare prodotti personalizzati, studiando e progettando utensili e attrezzature specifiche per le esigenze delle aziende.
Inoltre, abbiamo introdotto servizi di gestione di magazzini e logistica, attraverso GLogistics, società che consente alle realtà produttive di terziarizzare la gestione dei loro magazzini e concentrarsi sul proprio core business». In questo ambito nasce e si concretizza il progetto che contribuisce a Fabbrica del Futuro. «Il nostro progetto di adozione della manifattura additiva è una parte fondamentale della nostra strategia di innovazione. La manifattura additiva, o stampa 3D, sta rivoluzionando il modo in cui i prodotti reali vengono realizzati. Il nostro obiettivo è fornire alle aziende gli strumenti e le conoscenze necessarie per sfruttare appieno questa tecnologia. Spesso le incontriamo aziende che hanno sentito parlare dell’additiva, ma non hanno l’esperienza o una conoscenza approfondita della tecnologia e dei numerosi materiali che si possono utilizzare. Proponiamo applicazioni idonee e strategiche della tecnologia, perché, se impiegata correttamente, può portare a una riduzione significativa dei tempi e dei costi di produzione, oltre a consentire la realizzazione di oggetti complessi e sostenibili».
I risultati sono eccezionali nelle aziende che hanno adottato la manifattura additiva in modo strategico: «La produzione di alcuni componenti è passata da alcune settimane a poche ore, con una riduzione dei costi e dei tempi di produzione dell’80-90% – afferma Grazioli – Questo si è tradotto in vantaggi significativi per le aziende, consentendo loro di realizzare componenti altamente customizzati e con geometrie complesse. L’analisi topologica ci permette di ottimizzare la disposizione del materiale, creando pezzi più leggeri e resistenti. La manifattura additiva si è dimostrata uno strumento potentissimo quando applicata con saggezza».
La manifattura additiva è una tecnologia in rapida evoluzione, ed è necessario rimanere al passo con i cambiamenti e identificare nuovi scenari di applicazione. «Supportiamo le aziende con corsi di formazione e altri servizi a valore aggiunto, come lo studio delle applicazioni e dei parametri di produzione o il design for addive manufacturing – ovvero la riprogettazione ottimizzata per la stampa 3D –, poiché vogliamo garantire che siano in grado di sfruttare appieno il potenziale della tecnologia».
Beretta: l’intelligenza artificiale per migliorare i processi e unire tradizione e tecnologia.
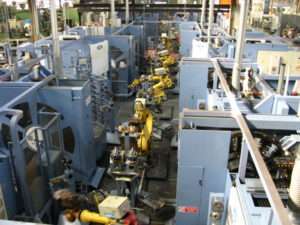
Il 2022 è stato un anno di record per Fabbrica d’Armi Pietro Beretta, che ha registrato un fatturato superiore ai 310 milioni di euro, a +23,7% sul 2021. Ciò grazie al forte impulso generato dall’ottimizzazione della produzione aziendale (mai così alta) e ai frutti che arrivano dalle politiche di industrializzazione e digitali intraprese. Nonostante restino gli Stati Uniti il mercato di riferimento, l’Italia ha visto aumentare il suo valore superando il 20 milioni di euro. A tutto vanno sommati i ricavi generati dal settore della Difesa. Fabbrica d’Armi Pietro Beretta è parte di Beretta Holding in cui Pietro Gussalli Beretta ricopre il ruolo di presidente.
La capogruppo, con sede in Lussemburgo, è stata creata il 22 dicembre del 1994 al fine di gestire lo sviluppo e il coordinamento strategico della più antica dinastia industriale al mondo, che si appresta a raggiungere il traguardo dei 500 anni di storia. Grazie all’impegno e alla visione internazionale, il Gruppo ora vanta 1,5 miliardi di euro di fatturato e oltre 6mila dipendenti dopo l’acquisizione, nell’agosto del 2022, del colosso europeo Ruag Ammotec, leader nella produzione e distribuzione di munizioni leggere. Fanno parte del Gruppo i marchi: Steiner, Sako, Tikka, Burris, Benelli, Franchi, Uberti, Stoeger, Chapuis, Holland&Holland e Centanex, SwissP, Norma, Rws e Mfs.
È negli anni ’80 che l’azienda assume le dimensioni attuale, grazie all’iniziativa del Cavalier Ugo Gussalli Beretta, quattordicesima generazione della famiglia, che imprime una forte spinta internazionale, aprendo una sede negli Stati Uniti, principale mercato del comparto armiero, portando la pistola 92FS a diventare nel 1985 arma ufficiale da fianco di tutte le Forze Armate statunitensi per trenta anni. Negli stessi anni nasce una linea di abbigliamento e accessori tecnici e per il tempo libero. Nel 1995 Beretta decide di aprire anche il canale “direct-to-consumer”: viene inaugurato il primo flagship store in Madison Avenue a New York. A questo hanno fatto seguito le “Beretta Gallery” attualmente presenti, oltre che a New York, anche a Dallas, Londra e Parigi.
La posizione di leadership, negli ultimi anni, è stata consolidata e amplificata dal figlio Franco Gussalli Beretta, attuale presidente di Fabbrica d’Armi Pietro Beretta – e fratello del già citato Pietro – che ha traghettato l’azienda verso il 4.0. L’impronta manageriale sempre più votata alle nuove tecnologie, a profondi e continui investimenti nell’innovazione per proporre prodotti d’eccellenza, alle contaminazioni con il mondo dell’arte e del lusso, fanno sì che Beretta sia un modello di business modernissimo a cui tutti guardano. Ma l’ingrediente segreto resta solo uno: la produzione di qualità senza compromessi insegnata da Bartolomeo cinque secoli fa. Sarà questa la stella polare che guiderà anche la sedicesima generazione e quelle a venire.
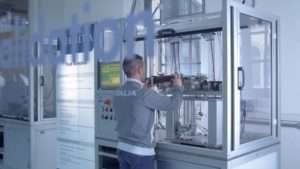
E quanto presentato in ambito di Fabbrica del Futuro è la sintesi di tutta questa storia. Si chiama “Beretta Intelligent Factory” ed è un progetto trasversale ai processi di Industria 4.0 già operativi in azienda, finalizzato allo sviluppo di soluzioni d’Intelligenza Artificiale in grado di supportare i processi industriali a elevata complessità attraverso l’analisi dei dati, affiancando l’Intelligenza Umana e valorizzandola. Si tratta di un lavoro d’equipe che ha attraversato gli snodi più preziosi dell’azienda. Due sono le iniziative che compongono il progetto: Event-base Prediction System, finalizzato al miglioramento dell’efficienza del sistema produttivo tramite l’evoluzione del sistema di manutenzione predittiva grazie alla messa a punto di un modello di basato su machine learning; e B-Wood, finalizzato al miglioramento del processo di classificazione estetica dei componenti in legno grazie ad un sistema basato su computer visione e deep learning.
I benefici sono sia strategici che economici. Dal punto di vista strategico, è in atto la creazione di competenze ed esperienze interne in ambito Intelligenza artificiale e la conseguente valorizzazione di dati come asset competitivo per migliorare il livello di oggettività e qualità delle decisioni; il tutto dosato dall’imprescindibile know how derivante dalla componente umana. Dal punto di vista economico, è stato registrato un aumento dell’O.E.E. (overall equipment effectiveness) che misura efficacia ed efficienza del sistema produttivo, oltre a una riduzione di errori, scarti e perdite. Conseguenza di ciò sono l’ottimizzazione di lead-time e time-to-market, oltre che il miglioramento del servizio al cliente. Il progetto non si limiterà alle due applicazioni già a regime, ma prevede di estendersi a diverse funzioni aziendali e nel lungo periodo.
Obiettivo primario è quello di dare impulso all’industrializzazione dei processi rendendoli, quindi, obiettivi. Esempi ne sono la prevenzione manutentiva ottimale e la classificazione dei componenti in legno: ambiti in cui alto è il peso economico e quindi necessari di elevatissimi livelli di efficienza. Ma la bellezza di questi progetti è la forte impronta umanistica: si tratta di una tecnologia progettata dall’uomo e messa a disposizione dell’uomo, che raccoglie un’esperienza di 500 anni di manifattura con una componente artigianale ancora forte ma necessariamente coniugata con criteri industriali.
di Laura Magna